
Schematic representation of ambient grinding, adapted
Once separated from the metallic material, ambient grinding is able to produce rubber crumbs with grain size ranging from 5 to 0.5 mm. Ambient grinding is the most commonly used and.Ambient vs. Cryogenic Rubber Grinding Eco Green ,89 After this initial break down step, there are three primary grinding methods that tire recyclers use. Ambient temperature grinding the first method developed, this type of CHAPTER 1 Grinding of Waste Rubber (RSC Publishing) ,Ambient grinding does not necessarily confine the temperature limit to a room temperature range. The processing temperature can reach up to 130 °C in the ambient grinding process. Ambient

Grinding and finishing processes ScienceDirect
201111 The three processes that have become established for highperformance grinding are: highperformance grinding with aluminum oxide (Al2 O 3) ‘conventional abrasive’ grinding Comparison between ambient and cryogenic ground ,It then uses a hammer mill to shatter the frozen rubber into smooth particles with a relatively lower area than the ambient grinding process [14]. [15] as the process of cooling or chillingGrinding Machine: Definition, Types, Parts, Working & ,A grinding machine or grinder is an industrial power tool that uses an abrasive wheel for cutting or removing the m aterial. It is a process of metal cutting by using a rotating abrasive whee l from
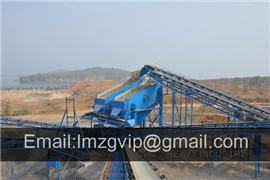
Process for ambient temperature grinding of soft polymers
According to this invention, there is now provided a process for grinding a soft and tacky polymeric material in the presence of a grinding aid at ambient temperature, wherein grinding TYPES OF GRINDING PROCESS UNDERSTANDING ,1127 Centerless grinding, as shown in figure, will be performed by locating the workpiece between one grinding wheel and one regulating wheel. Workpiece will be supported Grinding Process SpringerLink,Grinding Process, Fig. 3 Zones of elastic and plastic deformation in chip removal [ 16] Full size image During a machining process with a trackbound cutting edge engagement, the cutting edge of the grain penetrates the workpiece upon a flat path and, after a phase of elastic deformation, triggers plastic flow of the workpiece material (Fig. 3 ).

Grinding process
823 Internal grinding is done with the universal tool and cutter grinder with an internal grinding attachment (Figure 516). Note that the belt and pulleys are exposed; during actual operation, this area should be Grinding Processes SpringerLink,The finescale morphology of the surfaces generated by grinding consists mostly of overlapping scratches produced by the interaction of abrasive cutting points with the workpiece. An example of a typical ground surface is shown in Fig. 3.What is Grinding Process? ExtruDesign,529 The grinding process is truly a chip producing machining process. The grinding process can produce very accurate sizes, equally accurate geometry like flatness or circularity and a perfect surface finish. The grinding wheel is capable of machining hardened steel and even hardened highspeed steel, which other machining processes cannot do.
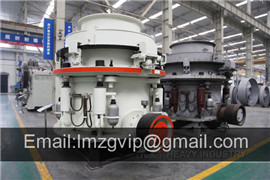
[PDF] Effect of cryogenic and ambient grinding on
In this communication, grinding characteristics of cinnamon (cv.Nityashree) and turmeric (cv. Pratibha) were investigated under cryogenic and ambient grinding conditions. Grinding of spices was carried out using a laboratory grinder with pin mill set up (M/s Hosakowa Alpine, Germany, Model: 100UPZ).What Is Grinding and Its Working Principle and Type?,928 Grinding process is a microprocessing method. Grinding uses a grinding tools and abrasive (a free abrasive) to generate relative movement between the processed surface of the workpiece and the grinding tool, and High Performance Grinding ScienceDirect,11 Figure 2: Performance characteristics of High Performance Grinding processes 4. Driving forces for HPG The main driving force for HPG processes is a steadily increasing economic pressure. Thus, an optimization of the whole process chain is desirable.

Topological Gear Grinding Methods
2014515 The process is set up in such a way as to attempt to adjust the contact line between workpiece and the grinding wheel to the nominal gear flank by correcting the position of one of the machine axes (Figure 14). Ultraprecision grinding ScienceDirect,201011 The machining of high precision parts by abrasive processes, however, is more difficult due to their complex and nondeterministic nature. In this sense ultraprecision grinding is primarily used to generate high quality and functional parts usually made from difficult to machine materials. The aim of ultraprecision grinding processes is toUnity】Postprocess后处理之Ambient Occlusion,1118 环境光遮蔽( ambient occlusion )的本质是计算在一个点的半球面范围内有多少方向被阻塞(如下图1.2.1),然后根据它调整表面颜色。 如果实时渲染使用的话非常消耗,所以在游戏中一般都使用(screenspace ambient occlusion ) 最近用 unity 5弄的一些渲染 wolf96的专栏 1万+ 9末。 。 。 要找工作了,,压力山大。 。 。 顺便求职(实习,明

TYPES OF GRINDING PROCESS Universal Grinding
1234 West 78 th Street Cleveland, Ohio 441021914. PHONE. 8883393006 Fax 2166315264. EMAIL. info@universalgrindingGrinding process,823 Grinding process Grinding is the process of removing metal by the application of abrasives which are bonded to form a rotating wheel. When the moving abrasive particles contact the workpiece, they act as tiny cutting tools, Ambient and Cryogenic Grinding of Fenugreek and Flow ,2013611 Angle of slide, volume, density of powder, Hausner ratio, Carr index, angles of repose and particle size distribution were determined at different moisture content ranging from 11 to 20% on dry basis for ambient and cryogenic grinding. Angle of slide for different planes was found to be increasing in the range of 39–60°.

Influence of Cryogenic and Ambient Grinding on Grinding
121 Grinding characteristics of fenugreek (cv. AM‐1) were carried out at cryogenic and ambient conditions. It was observed that it affected average particle size, volume surface mean diameter, mass mean diameter, volume mean diameter, specific surface of mixture, number of particles per gram, energy constants Rittinger and Kick's and specific energy consumption. TYPES OF GRINDING PROCESS UNDERSTANDING ,1127 Centerless grinding, as shown in figure, will be performed by locating the workpiece between one grinding wheel and one regulating wheel. Workpiece will be supported with the help of one guide or stop as shown in figure. There are three basic types of centerless grinding process as mentioned below. Throughfeed grinding Infeed grindingProcess for ambient temperature grinding of soft polymers,(a) introducing polymer pellets and a grinding aid into the grinding area of an attrition mill having counterrotating grinding elements operating at a combined tip speed of at least 170 m/sec, while passing air through the mill at a flow rate of at least about 350 m 3 per kg of polymer throughput, the amount of grinding aid being about 520%

Grinding Circuit Process Control
417 The form of this equation was: ln %+65 = K1 + K2 MFO + K3 MFW + K4 FOF %+65 = weight percent of plus sixtyfive mesh particles in cyclone overflow MFO = mass flow of ore to cyclones (tonnes/hour) MFW = mass flow Effect of Moisture Content on the Grinding Process and ,428 Grinding is an energy intensive process in which a hard matter is broken down. The consumption of energy for reducing the size of numerous types of agricultural and food materials increases when the size of the screen opening changes from coarser to finer and when an increase is present in the moisture content or material hardness [ 13 ].Frequent problems during grinding grindaix ,Grinding is a widespread production process and has long been a fixed part of almost every industrial production environment. During grinding, the parts (workpieces) are literally given the “final polish”. Grinding operations thus

The backend process: Step 3 Wafer backgrinding
The coarse grinding typically removes approximately 90 percent of the excess material. A typical twostep backgrinding operation will use dual spindles with grinding wheels mounted on each spindle. Scratches and Wafer Strength After backgrinding, the wafer will exhibit a scratch pattern on the backside (Figure 1a).,,