
How grinding mill design changed over the last 30 years
63 With the use of computers, the design of grinding mills has come a long way, mostly positive. As mill sizes get limited by manufacturing capabilities, the focus of the Grinding Mill an overview ScienceDirect Topics,The SAG mill was designed to treat 2,065 t h −1 of ore at a ball charge of 8% volume, total filling of 25% volume, and an operating mill speed of 74% of critical. The mill is fitted with Grinding Mill an overview ScienceDirect Topics,Fan mills are designed in the form of a centrifugal fan and therefore do not need a separate mill fan. Mills of this kind are commonly used for pulverizing lignite and similar fuels. In

Grinding Mill Design & Ball Mill Manufacturer
220 Grinding Mill Design. Morgardshammar started to design and deliver grinding mills in the beginning of the century. Today the mills are mill grinding technology design,116 Advantages of Hammer Mill 1. It produces specified top size without the need for a closedcircuit crushing system. 2. It produces relatively numerous size distributions with Grinding mills for mining and minerals processing,Fruitful Outotec Premier™ mills and Select™ mills are built with a robust design and components to eliminate unplanned downtime leading to high availability and reliability.

Attrition Grinding Mill Design Metallurgist
69 Attrition Grinding of Talc. The talc feed, which contained less than 10 percent minus 10micrometer particles, was ground to essentially all pass 10 micrometers in size (fig. 22). The bulk density of the ground Development of vertical stirred mill grinding disc and ,1130 Development of vertical grinding mill. The work concentrated on vertical grinding mill grinding efficiency development. It was studied what effect of disc design GTS Grinding Technologies and Systems Design and ,grinding test. G.T.S. provides at its headquarters a testing equipment for industrial grinding to test the process capacity and study the most suitable solutions. Moreover, G.T.S.

Milling GAW technologies GmbH
1125 Milling. Ultrafine grinding technology with the highest added value. Ground calcium carbonate (GCC) is used in papermaking as a filler as well as a coating pigment for surface finishing, whereby the ultimate Grinding Mill an overview ScienceDirect Topics,Fan mills are designed in the form of a centrifugal fan and therefore do not need a separate mill fan. Mills of this kind are commonly used for pulverizing lignite and similar fuels. In Poland, they are also used for grinding hard coal for hot water boilers. 2. Medium speed pulverizers (compression mills) n = 30–150 min−1mill grinding technology design,116 Advantages of Hammer Mill 1. It produces specified top size without the need for a closedcircuit crushing system. 2. It produces relatively numerous size distributions with a minimum of fines due to selfclassification. 3. It has a high reduction ratio and high capacity whether used for primary, secondary or tertiary grinding. 4.

Semiautogenous grinding (SAG) mill liner design and
200781 Nordell L.K., Potapov, A.Y., and Herbst, J.A., 2001, “Comminution simulation using discrete element method (DEM) approach—From single particle breakage to fullscale sag mill operation,” International Conference on Autogenous and Semiautogenous Grinding Technology (SAG2001), 30 September3 October, Vancouver, BC, Canada, Vol. 4, pp. 235–251.Attrition Grinding Mill Design Metallurgist,69 The variables having less influence on grinding efficiency and energy consumption were pulp temperature, design of rotor cage, clearance between the rotor and chamber bottom, rotorstator bar interval, additives, pulp level, Grinding technology Mischtechnik Mischer,The different types of mills are designed for the dry and wet grinding of brittle and soft to very hard materials. The selection of the right grinding system has a big influence on the profitability of the entire process as well as on the quality of the product. We develop a concept for you which is suitable for your individual application.

GRINDING TECHNOLOGY COURSE The Cement Institute
1017 The common cement grinding systems can be divided into three main groups: Ball Mill All grinding work is done in the ball mill, and the setup is: Ball mill in open circuit Ball mill in closed circuit with Mechanical air separator Rotor type separator Ball Mill with Pregrinding UnitVertical roller mills: The new leader in grinding ,1011 For companies wanting to establish that the VRM technology is the way forward, Loesche offers the mobile ore grinding plant (OGP) to run live tests on site. The OGP is a modular containerised comminution circuit laboratory Whirlwind mill fine and ultrafine grinding Grenzebach,The whirlwind mill has a simple, robust design. Thanks to its screenless design, users also benefit from low cleaning requirements. Maximum service life With its integrated rightleft running, the eddy current mill allows you to make optimal use of the service life of your grinding tools and wear protection segments.

Design, Installation, Commissioning and Operation of Fine
The demand for fine and ultrafine grinding associated with the processing of more challenging, finer grained orebodies and the global driver of minimising energy consumption has been an increased focus in our industry. Outotec's stirred milling technology, the high intensity grinding mill (HIGmill), was launched in 2012 in response to this industry need. First Quantum Minerals Ltd ELB millGrind Multiple Technology Solution in one SetUp,Multiple technology solution in one setup The millGrind series is specially developed for the requirements of machining in the turbine industry as multiple technology solution in one setup. The modular machine system in travelling table design allows an individual configuration of the machine according to the customers' needs.mill grinding technology design,116 Advantages of Hammer Mill 1. It produces specified top size without the need for a closedcircuit crushing system. 2. It produces relatively numerous size distributions with a minimum of fines due to selfclassification. 3. It has a high reduction ratio and high capacity whether used for primary, secondary or tertiary grinding. 4.

How grinding mill design changed over the last 30 years
63 With the use of computers, the design of grinding mills has come a long way, mostly positive. As mill sizes get limited by manufacturing capabilities, the focus of the design process has shifted from pushing the envelope to creating tools to do it cheaper and faster. Design workforce is becoming more global.Development of vertical stirred mill grinding disc and ,1130 Development of vertical grinding mill. The work concentrated on vertical grinding mill grinding efficiency development. It was studied what effect of disc design and position within the mill has to the grinding efficiency. How the grinding media behaves over time within the vertical grinding mill. Also the scaleup from laboratory to plant sizeAttrition Grinding Mill Design Metallurgist,69 The variables having less influence on grinding efficiency and energy consumption were pulp temperature, design of rotor cage, clearance between the rotor and chamber bottom, rotorstator bar interval, additives, pulp level,

Large vertical grinding mill working principle and structure
Through indepth development of new paths of industryuniversityresearch development, the introduction of advanced pulverizing technology, and continuous promotion of product and technological innovation, JHM Machienry has produced a series of coal mills, bentonite mills, and titanium dioxide mills.Semiautogenous grinding (SAG) mill liner design and ,200781 Nordell L.K., Potapov, A.Y., and Herbst, J.A., 2001, “Comminution simulation using discrete element method (DEM) approach—From single particle breakage to fullscale sag mill operation,” International Conference on Autogenous and Semiautogenous Grinding Technology (SAG2001), 30 September3 October, Vancouver, BC, Canada, Vol. 4, pp. 235–251.干磨机 Schenck Process申克集团,Raymond® Hybrid Turbine Classifier for RB Bowl Mills Raymond® Fine Grinding Roller Mill 流程图 Steel Plant Process Mini Mill Steel Plant Process Integrated Mill Gypsum Milling Process Flow Sheet Scrap Yard, Steelworks, Casting House, Rolling Mill Flow
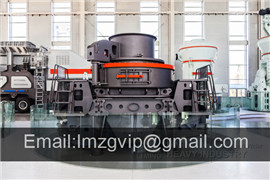
Grinding Mills Technology Trends
Grinding Mills. A grinding mill is a unit operation designed to break a solid material into smaller pieces. There are many different types of grinding mills and many types of materials processed in them. Historically mills were powered by hand (mortar and pestle), working animal (horse mill), wind (windmill) or water (watermill).Design of clinker grinding system; mill and ,Figure 1 presents the design of the clinker grinding system (closed circuit), which consists of a twochamber ball mill and the separator (Plasari and T heraska, 19 81). Cement clinker is usually(PDF) Grinding in Ball Mills: Modeling and ,201261 The central purpose of grinding models is to obtain mathematical relationships between the size of the feed and the size of the product (Monov et al., 2012). Size reduction is a result of three.